Electromechanical Assemblies in Defense Applications: Ensuring Durability and Compliance
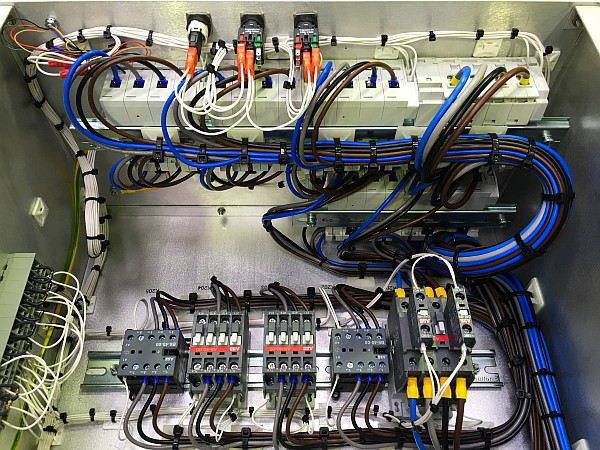
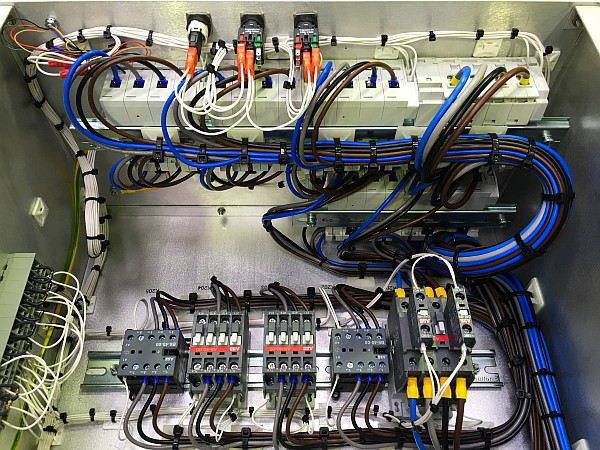
Electromechanical assemblies play an integral role in modern defense and military equipment. From advanced communication systems to unmanned aerial vehicles (UAVs) and missile guidance systems, these assemblies form the backbone of high-performance defense technologies. Given their critical role in national security, these components must meet stringent durability standards and comply with a variety of regulations, such as International Traffic in Arms Regulations (ITAR). Ensuring that electromechanical assemblies meet these demanding requirements involves a combination of meticulous design, rigorous testing, and adherence to regulatory standards.
The Importance of Electromechanical Assemblies in Defense
Electromechanical assemblies refer to the combination of electrical and mechanical components that work together to perform specific functions. These assemblies are often custom-designed to fit the unique requirements of defense systems, making them highly specialized. They encompass a wide range of applications, including power distribution systems, weapon control interfaces, radar and sonar systems, and avionics control systems.
In defense applications, electromechanical assemblies must function flawlessly in harsh environments, including extreme temperatures, vibrations, humidity, and exposure to various electromagnetic interferences. Any malfunction or failure in these systems can compromise the safety of military personnel and the success of a mission. Therefore, durability and reliability are paramount in every aspect of the design and manufacturing process.
Ensuring Durability in Harsh Environments
Durability is one of the foremost concerns when developing electromechanical assemblies for defense applications. These systems are often deployed in environments where they are subject to severe physical stresses. For example, equipment used in fighter jets or military ground vehicles must withstand high levels of vibration and mechanical shock. Similarly, assemblies used in submarines or naval vessels need to operate reliably in high-humidity and corrosive environments. The durability of these systems ensures mission readiness and minimizes the risk of equipment failure during critical operations.
To ensure that these assemblies can endure such conditions, manufacturers utilize high-grade materials and robust design techniques. Military-grade metals, plastics, and other components are selected based on their resistance to wear, corrosion, and fatigue. Additionally, the manufacturing process may include techniques like conformal coating or potting, where sensitive electronic components are encased in protective materials to shield them from environmental hazards like moisture, dust, and vibrations.
Rigorous testing is also a fundamental part of ensuring durability. Electromechanical assemblies undergo extensive stress testing, including thermal cycling, vibration testing, and salt fog exposure tests. These tests simulate the extreme conditions the assemblies will face in real-world defense environments, ensuring that they meet the required performance standards. Only those assemblies that pass these tests are deemed fit for military use.
ITAR Compliance and Regulatory Standards
In addition to durability, compliance with regulatory standards such as ITAR is crucial when manufacturing electromechanical assemblies for defense applications. ITAR is a set of regulations enforced by the U.S. Department of State that governs the export and import of defense-related materials and services. It is designed to protect national security by ensuring that sensitive military technologies do not fall into the wrong hands.
For manufacturers of electromechanical assemblies, ITAR compliance is a complex and necessary process. Companies must be registered with the U.S. government and implement strict protocols to control the flow of information and materials associated with defense-related projects. This includes controlling access to technical data, ensuring that only authorized personnel handle sensitive materials, and maintaining detailed records of all transactions involving defense-related technologies.
ITAR compliance also extends to the supply chain. All suppliers and subcontractors involved in the production of electromechanical assemblies for defense purposes must adhere to ITAR regulations. This ensures that the entire production process is secure and that no unauthorized parties have access to sensitive military technologies.
Beyond ITAR, defense manufacturers must comply with other regulations, such as MIL-SPEC (military specifications) and AS9100, which is the international quality management standard for the aerospace and defense industries. These standards ensure that all products meet the specific performance, quality, and safety requirements set forth by the U.S. Department of Defense (DoD) and other regulatory bodies. Adherence to these standards is essential for producing reliable electromechanical assemblies that can withstand the rigors of defense applications.
Quality Control and Testing Protocols
Meeting the high standards of durability and compliance requires robust quality control systems throughout the design and manufacturing process. Manufacturers typically implement advanced quality management systems that are tailored to the specific needs of defense-related projects. This includes detailed inspections at every stage of production, from initial design and prototyping to final assembly and testing.
In the case of electromechanical assemblies, functional testing is particularly important. This involves subjecting the assemblies to real-world operational conditions to verify that they perform as expected. Automated testing equipment is often used to assess the electrical and mechanical performance of the assemblies, while manual inspections are conducted to ensure that all components meet the required specifications.
Additionally, traceability is a key component of quality control in defense manufacturing. Manufacturers must maintain detailed records of all materials, components, and processes used in the production of electromechanical assemblies. This allows for rapid identification and correction of any issues that may arise during production or deployment.
Conclusion
Electromechanical assemblies are critical to the performance and success of modern defense systems. Ensuring their durability in harsh environments and compliance with regulatory standards like ITAR is essential for protecting national security and supporting the operational readiness of military forces. Through the use of high-grade materials, rigorous testing protocols, and adherence to stringent regulatory requirements, manufacturers of electromechanical assemblies play a vital role in delivering reliable and durable systems that are capable of performing in the most demanding defense applications.